シリコーンゴムのバックラインディング現象
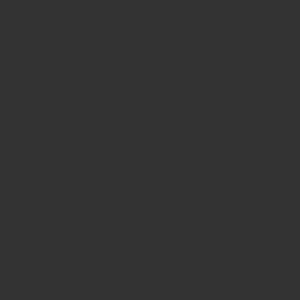
シリコーンゴムは流動性が比較的良いゴムなので バックラインディングは起こりづらいのですが 体積が大きいボリューミーな製品や 金型の隅まで材料が流れ込むまで時間が掛かるような狭窄形状な製品に発生することがあります。特に硬度が柔らかい材料を使うと発生しやすいです。
バックラインディングとは?(バックラインド)
バックラインディングとは(バックラインド)ブロック状の製品や円筒状の製品で 金型割部分のパーティングラインに亀裂や裂けが生じる不規則な凹形状になる現象です。
金型に接している材料表層と材料内部の温度差から加硫する速度の違いで 製品外部は固まりはじめているのに 内部は温度上昇が遅れて 時間差で固まりはじめます。
内部が固まりだすと熱膨張で内圧が高まり、すでに固まっている外部に広がろうとする膨張圧力がかかります。この圧力で金型を開放した際に製品が膨らみ、この圧力の負荷を一番受けやすいパーティングラインが内圧に負けて破裂して裂けてしまう。
![]() |
![]() |
![]() |
![]() |
![]() |
![]() |
![]() |
![]() |
円筒状などの狭窄製品で縦置きに成形した場合、上部の細い部分から流れ込んだ材料が 下部まで流れた時点で上部が固まりはじめていると下部まで到達した材料との温度差が生じます。また材料の流動で上部に戻ろうとする圧力で ブロック状の時と同じような温度差、圧力差が生じて やはり一番負荷を受けやすいパーティングラインで破裂が生じます。
![]() |
![]() |
また、パーティングラインは仕込んだ材料の余った分が流出する出口でもあるため,限りなく狭窄になる部分でもあります。普通は余った材料が一気に流れ出るので製品部と固まる速度は同じになるので支障がありません。
しかしジワジワと材料が流れ出るような設定の場合は パーティングラインが狭窄のため流れ出る材料が一番固まりやすい部分です。流れ出た材料が固まっているのに さらに材料が流れ出てくると加硫の時間差でパーティングライン部分がきれいに成形されずに凸凹に形成されたりします。
バックラインディングが発生するメカニズム
![]() |
![]() |
![]() |
![]() |
原因
- 金型パーティングラインに発生する加硫スピード差によるヒケ
- 表層部と内部の加硫スピードの温度差
- 成形加硫開始温度設定の異常
- 材料の仕込み重量過多
- キャビティーからの材料フロー悪化
- 金型設計時の喰い切りクリアランス設定の不足
対策
- 金型表面温度を下げる
- 仕込み材をスコーチしない程度に予熱する
- 仕込み重量を下限管理する
- 成形圧力は出来るだけ低く設定する
- バンピング設定は回数を増やし出来るだけ余材を排除する
- 金型喰い切りのクリアランスは可能な限り大きく(広め)設計する(拡大図)
- 金型喰い切りのクリアランス不足時は適正なクリアランスを確保できるように金型改造修正を実施する
ある程度は図面を見た際にバックラインディングの発生は推測できます。
まずは金型起工時に喰い切り設計や材料の流動を予想して材料の逃げ溝や捨て溝などを設計しておくことが必要です。
ブロック状や狭窄部がある製品では 金型温度を低くして加硫時間を長くする手法にはなるので、出来高減少によるコスト増が副作用として生じます。
また、30°以下の低硬度シリコーンゴムでは いろいろな対策を講じてもバックラインディングが抑えられず製造不可の場合があります。特に5°10°では5mm以上のボリュームがあると大きな懸念点になりますのでご了承ください。
お問い合わせ
他にもこんな記事が読まれています
樹脂の射出成形で起きやすい「ウエルド」「ヒケ」「焼け」などの現象は比較的シリコーンゴム成形では起きづらい現象です。大きな理由としては 樹脂は溶かした樹脂材を金型の中で冷やして固めるため 材料の流動性と固まるスピードのコントロールが難しいので[…]
一般的なゴムは熱と圧力で熱硬化させます。このことを加硫・架橋と呼びます。一部の液状シリコーンゴムなどは自然硬化するタイプもあります。プラスチックは原材料を溶かして金型内で冷やして固めますが ゴムの場合は熱を加えて固めます。 加硫と架橋(パ[…]
ゴム金型の構造は独特な設計基準で作成されます。各社のノウハウが盛り込まれます。これが会社の技術力に繋がっています。特にバリ発生の仕組みや金型表面状態、メッキの役割、「喰い切り溝」が付いた独特な金型構造を紹介します。 プラスチック成形で[…]